Rendered walls
Rendered Surfaces
Standard Rendering is based on three basic elements: 1 gypsum cement : 1 hydrated lime : 6 Sharpe sand and applied by trowel to a smooth finish.
Other methods of application by spray produce textured finishes some of which are self coloured and do not need painting.
There is a range of products available and can be oil or water based and include smooth coatings to heavy textured finishes.
Once decided on the type of finish required and paint brand obtain the products data sheet of the company's website and confirm it meets with your requirements.
Preparation for all coatings.
Ensure the surface is dry and free from all dust, dirt, loose material and surface contaminates.
Apply the priming/sealer coat and finishing coats in accordance with the manufactures instructions.
Manufactures including the following offer a range of suitable products.
Andura Coatings. https://www.andura.com Tel. 01869 240374
Dulux Trade. https://www.duluxtradepaintexpert.co.uk
Johnstones. https://www.johnstonestrade.com/products
Brickwork
Brickwork.
In general the bricks used for normal building works are:
Commons which are dense and smooth. To paint this type of brick is not straight forward as keying onto the brick surface can be difficult.
Because of this, the surface needs to be keyed and this can be done by either sweep sand basting or acid etching.
Once the surface preparation has been carried out and the surface is clean, dry, and free from other surface contaminates, the selected paint manufacturers masonry paint can be applied by following their specific recommendations.
Andura Coatings. https://www.andura.com
Dulux Trade. https://www.duluxtradepaintexpert.co.uk
Johnstones. https://www.johnstonestrade.com/product/pliolite-based-masonry-finish https://www.johnstonestrade.com/products
Sandtex. https://www.sandtexpaints.com/uk/masonry-paint/ https://www.sandtex.co.uk
Corroded Aluminum
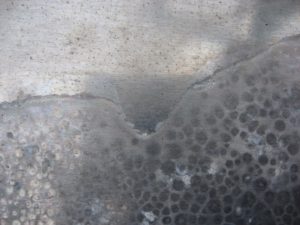
Aluminum is used for many projects within the building and construction industry.
While it is relatively free from corrosion paint coatings applied at the factory is often required.
See: Powder Coating and Coil Coating
New aluminum sheeting which requires on site painting the specification would be as that for Galvanised Steel.
See: Specifications: Galvanised Steel.
uPVC (Un-plasticised Polyvinyl Chloride)
uPVC (Un-plasticised Polyvinyl Chloride)
Specification.
Only weather items should be considered for repainting.
Surface preparation.
All surfaces should be thoroughly washed down to remove all dust, dirt. All signs of organic growths, mould or algae should be treated with a fungicidal solution applied in accordance with the manufactures instructions.
Wash with fresh water and leave the surface clean and free from any surface contaminates.
Pre-painting.
Wipe down with Methylated spirit and allow to dry.
Note: Do not abrade the surface or clean with strong solvents.
Painting
Paint manufactures offer water based systems for uPVC, therefore, the selected supplier’s product data sheet should be check before use. Some systems are self-finishing which is a primer, undercoat and finish all in one.
Marine Plywood
Marine plywood
Marine Plywood is manufactured from durable face and core veneers, with few defects and each layer of veneer is bonded with a high performance resin.
The paint systems available from specialist suppliers are based on high performance epoxy and polyurethane coatings.
Due to the construction and quality of marine ply it is suitable for use in areas of high humidity when treated with the appropriate paint products.
https://www.international-marine.com/
https://www.hempel.co.uk/en-GB/marine
https://www.awlgrip.com/region-selection?destination=products
https://www.youtube.com/watch?v=eF5LVBW1vl8
Hardwood Painting
Hardwood specification.
General.
In the building and construction industry the two most common hardwoods used are Oak and Chestnut.
For exposed timber structures and for internal components such as doors and trim work, Oak is selected. While Chestnut is used for areas such as exterior cladding.
Both of these wood species contain Tannin (tannic acid) and when use under dry conditions present no problems. However, if the timber surface comes in contact with moisture the acid can be activated and comes to the surface.
If the woods have been painted with a conventional alkyd oil paint then tannin bleeding can occur causing the paint coating to yellow.
See: Yellowing in Problems and Solutions.
To prevent this the following generic specification can be considered.
Preparation.
The bare timber should be sanded down with suitable grade sandpaper to a smooth finish. Any hard surface resin from wood knots or sap residue should be removed by the most appropriate means.
Remove all other surface contaminates as required leaving the surface clean and dry.
Areas around wood knots and sap residue should be wiped over with methylated spirit and allowed to dry.
Priming
Priming coats for hardwood vary from different manufactures which included acrylic resin, spirit and alkyd based aluminum primers.
Undercoat and finishes.
For compatibility it is necessary to follow the selected paint manufacturers instruction.
Note:
Manufactures may recommend using a heat source to draw the resin to the surface to remove the resin but if the resin pocket is deep this may not be successful.
Cutting out knots or replacing a section of the timber may be required. See: Resin Exudation in Problems and Remedies
Ferrous Metal
General.
When hot molten steelwork is milled and rolled to profile required such as stanchions and girders as the steel passes through the rollers a thin film of oxide is left on the surface and this is known as mill scale.
This sacrificial layer of oxide must be removed before painting and can be carried out using various methods such as grit/sand blasting (Also known as abrasive blasting) or Needle Gun.
If the steelwork is allowed to weather and all that is left on the surface is rust, then this can be successfully removed by hand and or mechanical wire brushes.
Preparation
Once the appropriate preparation work has been carried out leaving the surface dry free from all contaminates then painting can proceed.
Note: if the surface is prepared byway of Grit/sand blasting then priming should commence immediately and before oxidisation of the steel surface takes place.
Priming.
While a Zinc Phosphate metal primer is generally recommended, paint manufactures do offer others, including: General Purpose primers for wood and metal, Water based modified Acrylic based along with single and two pack epoxy paints which are high performance coatings.
It is always advisable to contact your preferred paint supplier to obtain the appropriate data sheet to establish their recommendations and painting system .
Where the usage requires a chemical resistant coatings, information should be obtained from manufactures who specialise in high performance coatings such as:
Sherwin-Williams (Leighs) https://www.swpaintsonline.com/
https://www.akzonobel.co.uk
https://www.youtube.com/watch?v=2hguRUF0P4A
Masonry New - Smooth Finishes
Masonry Paint onto New Work.
Remove all mortar splashes, make good where necessary with the appropriate external plaster filler. Ensure the surface is dry, clean and free from surface contaminates; mould, lichen. and efflorescence.
Traditional common bricks (Fletton) and polished concrete should be acid washed (hydrochloric) or sweet blasted to obtain a suitable key for painting.
Painting
Generically, onto new work all systems would require 1 sealer coat followed by 2 full coats of the masonry paint.
Manufactures products can vary from, modified PVA external coatings, Acrylic based paints, modified Silicone based coats and oil coatings based on Pliolite®resin.
As painting systems vary from different manufactures reference should be made to their product data sheet to ensure it meets with the required performance.
Note:
See problems and Remedies Carbonation of Concrete.
Pliolite ® trademark is registered to Goodyear Tyre and Rubber company.
Suppliers of Masonry finishes include:
Andura Coatings. https://www.andura.com
Johnstone Paints. https://www.johnstonestrade.com
International Paints. https://international.brand.akzonobel.com
Dulux Paints. https://www.duluxtradepaintexpert.co.uk
Galvanized Steel
General.
New Galvanised steel is one of the most difficult substrates to paint, therefore, correct surface preparation is paramount.
Galvanised surfaces will last for many years untreated and when exposed to the elements the bright finish will lose its brightness and tone down to a matt grey finish.
If weathering has taken place then the pre-treatment of the surface before painting may be different from that stated below.
Paint manufacturers offer different systems for painting galvanised steel and other non ferrous metals, therefore, they should be contacted and their recommendations strictly followed.
The following information is generic and for guidance only.
System and products,
Preparation.
Degrease with a suitable degreasing agent, methylated spirit or other cleaning solvents. For small areas hand etching with a suitable abrasive paper or cloth will improve the surface key. For large areas sweep blasting the surface to obtain a fine textured profile will provide a good surface for subsequent painting.
Mordant solution (T-Wash) should be applied to the prepared surface which on drying turns the bright metal surface black confirming the surface is clean and free from all contaminates.
Pre-treatment of galvanised surfaces
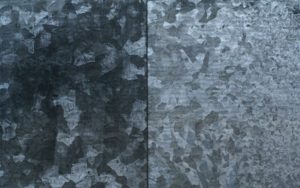
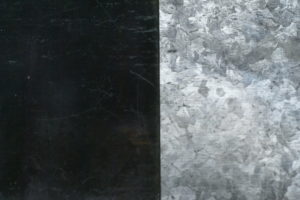
Priming
Products depending on manufacturer.
Priming coats can be either PVB Self etch primer, Zinc phosphate or general purpose primers. Undercoats and finishing materials can be oil or water based along with high performance epoxy and polyurethane protective coatings. Fire protection finishes are also specified.
Once the performance requirements have been decided, the manufacturers product data sheet should be obtained and instructions followed.
Note: PVB Self etch primers are susceptible to moisture and should be overcoated as soon as possible without exposure to high humidity or rain. Also the dry paint film is translucent so it is important to ensure the entire surface is coated.
In cases where painting of galvanised steelwork is required then steel fabricators often apply a holding primer before the steel is delivered to site. Under these circumstances it is important to establish what product had been used and consult the manufacturer for a recommended specification.
For further information on Zinc coated steel contact: British Galvanizers Association. 'What is Galvanizing-See:> https://www.galvanizing.org.uk/galvanizing-process/
Product illustrations provided by Bradite Limited. http://www.bradite.com
Dry Wood Rot
Wood Rot
Cause
Wood Rot: comes in two forms Dry and Wet. (see wet rot)
Dry Rot. The term implies that the timber is in a dry condition but it would normally have a moisture content reading of approximately 28%.
This along with a damp humid environment can lead to fungal growths forming on the timber.
Once the fungi spores /growths are established even though the moisture content of the wood has dropped and the cause remedied, the spores can still survive if the moisture content in the timber is still around 20%.
The fungi feeds on the wood and extracts the moisture/water which results in the wood structure becoming dry and brittle.
Remedy
The affected areas should be treated as soon as possible as the fungi spores can quickly spread. In domestic situations dry rot can often be found under floorboards at ground level where the air bricks are blocked. Other areas can be unvented cellars and roof spaces.
In these cases the assistance of a specialist wood preserving company should be sought.
For further information and specific advice contact:
https://www.rentokil.co.uk or search for local contractors
For wood repair systems: www.repair-care.co.uk windowcaresystemsang