De-Natured Wood
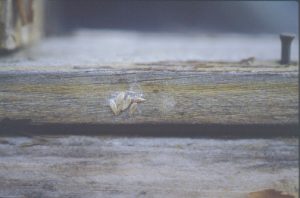
De-natured wood
Cause
Unprotected wood which has been exposed to the elements (U.V. light) and has become extremely dry causing a breakdown of the natural cells.
Solution
Mechanically sand down to remove the top layer of wood followed by priming with an oily wood primer. Standard primers if used should be thinned to obtain penetration of the wood,
Standard alkyd systems can then be applied.
NB. If the de-natured wood is not removed and replaced then further paint failures are likely.
Organic Growths. Lichen, Algae, Mould.
Lichen/ algae organic growth
There many Types of Lichen and can be present in different colours including grey, orange, red, black, yellow or green. Lichens normally form a crust like surface on the surface.
Algae is normally green in colour although can also be black, red, orange or yellow and forms a matt- like film on the surface or streaks down the surface.
Fungi colours can be black, orange, yellow, red or brown and form as a film or spots.
Cause
Generally occurs in conditions where the surface remains damp and to the northerly and westerly elevations.
Textured surfaces are more prone to holding moisture than smooth surfaces
When present on exterior surfaces, it is most likely to be associated with moisture in the substrate and lack of air flow; close proximity to trees can also be the cause.
Lichen on interior walls is due to heavy condensation and the lack of air flow
Solution
For exterior walls power wash to remove all mould / algae back to a clean surface. It may be necessary to pressure wash or light sand blasting.
Apply two coats of recommended fungicidal wash, allow 24 hours drying between coats and allow the surface to dry out.
Apply selected manufactures masonry finish in accordance with their recommended instructions.
For interior walls remove by heavy scrubbing and washing with a solution of bleach and or a proprietary fungicidal wash back to a clean surface. Once the surface has dried then apply the selected wall finish strictly in accordance with manufactures instructions.
Plywood Checking
Plywood Checking
Cause
Breakdown of a paint system applied to plywood which has “checked” (the ply surface splitting) allowing moisture to enter and causing detachment of the paint coatings.
Solution
Scrape back to a firm edge by removing all loose and defective paint. A system based on glass fibre weave membrane may help to overcome further problems. Textured paints have proven to be more successful on this type of substrate than smooth coatings.
Galvanized Steel Flaking
Galvanised steel flaking
Cause
The surface of new galvanised (zinc coated steel) sis is very smooth, therefore , if to be painted the steelwork prior to painting requires special preparation. If not then the adhesion onto the untreated surface will be suspect and ultimately flaking of the applied coatings can occur.
Solution
All the defective coatings should be removed back to the zinc coated steel.
The most effective method is to have the surface prepared by sweep blasting to remove all defective paint. This is carried out by specialist contractors who use grit or sand to produce a fine texture surface without penetrating the zinc coating.
If the above is not possible then removing the flaking paint coating can be done by chemical or mechanical means; the exact method will depend on the nature of the paint coating which has been applied. The resultant surface should be prepared to provide a suitable key for priming coats.
How can I tell if the steel is galvanised?
The galvanised zinc coated finish is non-metallic therefore using a normal magnet will confirm.
See galvanised specification
For further information: What is steel Galvanized Steel: https://www.galvanizing.org.uk/galvanizing-process/
Wood Stain Algae
Wood Stain Algae
Staining
Cause
Organic growths as a result of the timber having been exposed to rain water with the moisture content in the wood remaining high. Most prevalent when shaded from direct sun light.
Remedy
Once the staining has occurred, thorough sanding down is needed to remove all the surface contaminates back to bare timber followed by washing down with a fungicidal solution and allowed to dry, followed by recoating with the selected wood finish in accordance with manufacturers instructions.
Note: If it has not been possible to remove all the discolouration then a darker shade of finishing colour will have to be considered.
Alternatively an opaque microporous coating could be considered.
Discolouration - Yellowing
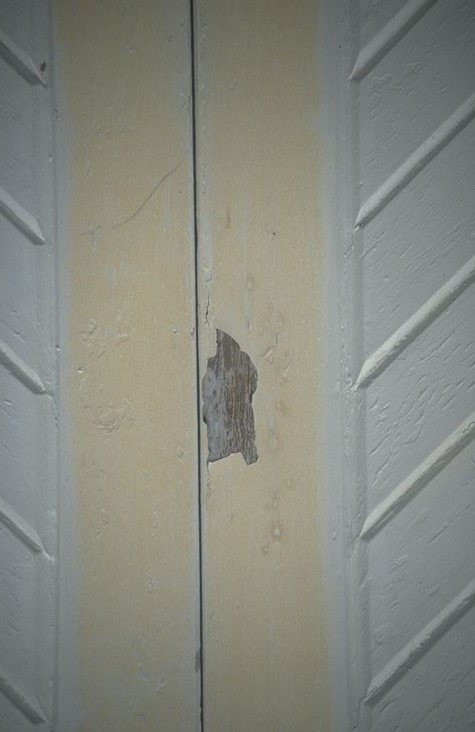
Discolouration : See Yellowing.
.
Flaking of Stained Wood Finishings
Flaking of stained wood finishes
Cause
Stained wood finishes are translucent/semi transparent.
The applied dry film thickness of these coatings are less than that of a traditional opaque paint finish.
These coatings, particularly light colours, can be affected by ultra violet rays that penetrate the dry film causing the underlying wood to become very dry and fibrous. The performance of translucent wood finishes can vary and special attention should be given particularly to exposed areas such a southerly elevations. For this reason window sills and styles may require attention and re-coating sooner than expected which in some cases can be every six months.
Note: On new building works were the timber items such as windows come to site with an initial stain coating applied they should recoated as soon as possible as the factory applied finish may not protect the underlying substrate from UV rays and can cause degradation of the timber fibers.
Remedy
All the defective coatings should be removed back to bare wood. This should be followed by thoroughly sanding down back to sound wood. All knots and sap residue should be coated with clear shellac knotting. Any areas of wood which need replacing due to damage, should be repaired using a suitable wood repair material. For glazing, linseed oil putty should be avoided and a suitable butyl glazing sealant used. Where repair fillers have been used there may be a slight colour difference. As these wood finishes are semi-translucent any difference in the colour of the surface to be coated will mirror through the newly applied coating. A test area should be carried out as it may be necessary to tint the first coat to match or use a slightly different shade. For redecoration work, if possible, always use the same manufacturers’ product and recommendations.
Repair Care. www.repair-care.co.uk
Available from all leading Paint manufacturers Trade stores and Decorators Merchants including:
Brewers Decorating Centres. - https://www.brewers.co.uk/stores
PaintWell - https://paintwell.co.uk/storelocator
Flocculation
. Flocculation (floating)
Cause
Flocculation (floating) is caused when the pigments have not been dispersed correctly during the manufacturing process. It can also occur if the product is obtained from a supplier who has used a colour tinting machine to provide the shade required. And the mixing/agitation of the paint has not been sufficient to disperse the added colourants.
Remedy
If the paint product was factory made and tinted it would not be possible to have this dispersion rectified, therefore, a new batch would be required. If the product has been mixed by an independent supplier, then it may be possible to have the paint agitated again to disperse the colourants properly. When more than one tin of the same colour is obtained and mixed at source, each tin supplied should be boxed together before use to ensure uniformity of colour.
Flocculation is a manufacturing fault
Masonry Rust Spotting
Masonry Rust Spotting
Cause
This staining is caused by iron oxide being present in the sand content of the stucco finish mix and is activated by moisture coming into contact with oxide particles.
Solution
Ensure the surface is completely dry and apply a suitable sealer to the affected areas which would normally be oil or spirit based. If a standard water based masonry finish is to be applied and a stabilising solution has been used and the finish is glossy glossy finish then this should abraded to provide a suitable key.
Where rust staining is present it is recommended to use an oil based masonry paint based on Pliolite® (Goodyear Tyre & Rubber Co. Inc) resin.