Problems Never Leave Us
Post under construction
Some problems never leave us.
Ongoing issue with applying modern water based paints over existing under bound /chalk coatings such as Lime Wash and Distemper.
After decades of experience, specifiers are still firefighting known problem relating to flaking have failed to fully address the issue to eliminate the root cause to prevent the recurrence of this issue.
The use of Lime wash goes back as far 7500BC. In the mid 1800 Distemper as a commercial coating was launched by, The Wall Paper Manufactures Company, located in Darwen Lancashire. Initially this was marketed as Hollins Distemper then changed to WalPapMur and then Walparmur.
At his time if a more durable, washable was required the chalky coating would be overcoated with a thinned down coat of of Linseed Oil and Turpentine
to consolidate the chalky finish.
Following the two world wars and the extensive building projects Walparmur was the brand leader for coating ceiling and walls up to the time when water based emulsion paints were introduced in the late 1940 and early 1950’s.
When this new emulsion paint was introduced and used to overcoat lime or distemper surfaces in place of the original linseed oil based sealer,
manactures introduced a clear or slightly tinted alkyd product to consolidate the chalky, powdery surfaces.
At this time specifications for this new sealer coating was generally quoted as a stabilising solution and should be brush applied whereby the brushing action was worked into the under bound chalky substrate to provided a stable base for subsequent water or oil based coatings.
Only too frequently the use of this stabilising solution was incorrectly specified as it was considered that any surface which looked suspect such as: cracks or surface spalling would need to be stabilised even though the surface condition was not chalky or porous. (see: Paintcheckplus News ‘Stabilising or Not’
Photo 1: Where a stabilising solution has been applied to a nonporous surface resulting in the finish being glossy consequently the adhesion of water based masonry finishing being poor.
One major factor often overlooked is the weight to the overall thickness of the paint coatings.
On average the weight of 5 litres of water based emulsion/acrylic wall paint varies between 6.5 and 7 Kilograms, the differential relating to the solids content of the individual product.
As an example the weight of 5 litres of paint (minus the tin) is 6.5KG although this will vary between manufactures.
Using combined data from several manufactures looking at the volume solids, wet film thickness, dry film thickness and
the manufactures recommended spreading rate per litre, the dry weight per m² of the applied material can be calculated
along with the expected film thickness. This on average for water based materials is 30µ micrometres. Based on the
average dry film thickness of 30µ micrometres per coat being calculated and compared with the sample removed from
site was 629µ micrometres which equated to 21 single coats of paint.
In this instance the specifier has not taken the weight of the film thickness into consideration.
Rather than produce a planned maintenance programme the authority decided on a patch and repair procedure.
The Problem Continues
Until specifiers stop addressing just the problem at face value and don’t look at the underlying cause of the problem continues…….
NB. The illustrations shown were taken in 2022 from a building which dates back to 1942.
Paintcheckplus, has been produced in a digital format for immediate access and reference at a one off life time subscription to include all future additions and updated.
A Step Too Far
A Step Too Far
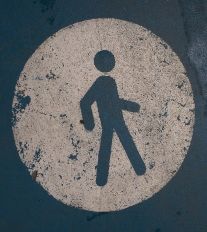
The ‘Waymarkings’ were applied to a newly laid concrete surface, but soon after the areas were commissioned, but after a matter of a few weeks the erosion of the paint coating became apparent.
As the parties involved could not agree as the cause of the erosion, it was agreed to employ the services of an independent coating consultant.
Examination of the paint coating sample.
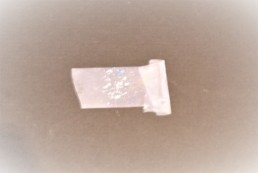
Reverse side of the sample removed showing latent cement particles attached to the reverse side of the paint film.
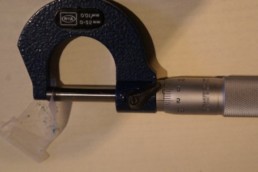
Film thickness of the tape use
50 ᶣ micrometres

Film thickness including paint, cementous residue and tape =70µ micrometres
Further examination of the sample was carried out under the microscope
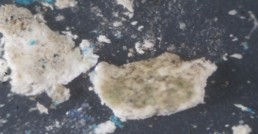
Reverse side of the sample showing latent
Cementitious particle attached to the paint film.
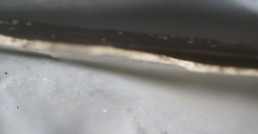
Cross section of the removed sample showing the degree of cementitious material and the thin line showing the paint film.
Conclusion.
Although the concrete flooring was new with a polished float finish there was no preparatory work carried out to ensure any latent material was not present. The contractor had to prepare and recoat at his cost.
Emulsions - Touching up
In todays contractual world we find only too often that the decorating operation is carried out long before it should be. We all know that the finishing trades are having to work side by side because time schedules for completing contracts have been drastically reduced. Many site managers and their superiors think that when a coat of paint goes on they are nearing the end of the contract, but we all know how untrue this is. This has resulted in the decorating trade being called in far too early. We know many share this view but cannot do anything but agree to the instructions by those who ultimately pay the bill. It is inevitable that when painters are working around other trades, damage to finished work will occur.
On many sites it seems to be the norm that if a door or any other fitting is damaged then the appropriate tradesman goes back and is paid for the additional costs incurred. When it comes to decorating, many expect the painters to go back to repair damaged work at their expense. This is unreasonable because it is generally poor site management and enforced working conditions that caused it in the first place.With regard to 'touching up' there are several aspects that should be considered. These are the specification, grade and type of emulsion, the method of application and finally the manner in which the 'touching up' is carried out.
Specifications, as we are only too aware, are always minimal and, depending on the grade and type of product being used, can consist of either one sealer and/or one finishing material. In the majority of cases it is reasonable to assume application is generally by roller.
However for large areas of work, application is often by spray, airless or HVLP units.
While either method of application produces a satisfactory finish, an initial problem can occur when 'cutting in' by brush around the ceiling line , light fixtures and wall perimeters. Normally a three or four inch brush is used and the material is applied in a band of two to five inches. This is often left to dry before the remaining areas are filled in.
As a result we have two different finishes on one surface. The area applied by brush can be slightly heavy due to the operator 'laying on' the material to obtain maximum obliteration, resulting in the finish being ropey with tramlines. The other areas will appear slightly mottled or textured depending on the method of application i.e. spray or roller.
Spray application generally produces an even finish and, depending on the type of material and skill of the operator, a satisfactory finish can be produced in a minimum number of coats. Roller application however can cause problems due to the different types of roller sleeves available. The finish produced can vary from a fine rippled effect to a heavy texture. The viscosity of the paint being used also has a direct bearing on the appearance of the finished film.
To try to limit the variations between the cutting in and the roller application it is much preferred that the two coats of paint are still wet thereby enabling a degree of blending to take place.
Damage to the finished paint surface is generally surface marking and for speed and economy the painter endeavours to cover in one coat, often applying too thick a film to achieve maximum coverage. Where damage to the surface necessitates making good with fine gypsum plaster these areas when 'touched in' are often visible because the texture and porosity are different to the adjacent surface. The light reflection off the different
surfaces instantly highlights the 'touching up'. In addition to this, material from a different product batch is often used and because of a slight variance in batch to batch colour matching blending does not take place. It should be recognised that with colours supplied through a tinting system, variation can occur - some manufacturers do state that each tin tinted should be considered to be a different batch. In addition to these two aspects areas of 'touching up' can also appear sheary. Colour can also play a major part as to whether or not these repaired areas will be seen with white and very pastel tints being less noticeable than the medium to dark shades. These problems can occur even though material from the same batch has been used for 'touching up'. The conclusion therefore is that no one should expect areas that have been damaged to be readily 'touched up' and if this operation is necessary then these areas should be re-coated using the same method as the original coats that were applied. At least there may be a better chance that these areas will be less noticeable.
Stabilising: A solution or Not
In the 1950's a new, revolutionary, washable material was developed to replace the then traditional non or semi-washable coatings. It was called emulsion paint.
But, it was soon established that when this product was applied over our very old favourites, distemper and limewash based coatings, problems occurred.
The prime difficulties encountered were caused during the drying period of the emulsion. This often caused a breakdown within the layer of an underbound material such as distemper. To combat this manufacturers introduced an oil based primer which in the very early days was based on a standard varnish with viscosity adjustment.
This very thin coating was then applied by brush helped to consolidate the top layer of the underbound material, and when dry it proved a sound surface to accept this new emulsion coating
Very soon the name Stabilising Solution was understood, accepted and introduced into the glossary of paint terms.
Distemper and limewash coatings are still available and used mainly on listed buildings but are rarely found these days in the course of normal refurbishment work.
Today it is only when excessive coats of emulsion or similar paints
have been applied to underbound or weak surfaces that problems may arise. A breakdown of the dry paint film is generally associated with the film weight and ageing of the
coatings applied over this underbound preparation, certain areas remain powdery or friable, it is only then that the Stabilising Solutions are recommended.
The term 'to stabilise' is often taken out of context. The need is often felt to 'stabilise' unpainted surfaces such as sand and cement render or paint coatings which are defective but not underbound.
This is wrong. In the majority of cases unpainted surfaces are not considered to be underbound or friable. Since the introduction of emulsion paints most surfaces which require re-painting, even though a breakdown may have occurred, do not require treatment with stabilising solution. As always there are exceptions to the rule, and manufacturer’s recommendations should always be followed.
Care should also be taken when bricks, particularly flettons, concrete and other non porous surfaces are to be decorated.
£5,700 TO CORRECT
The history associated with these illustrations is that the walls were sand: cement rendered onto an insulating block. Because of the combined construction, there was a difference in thermal movement. Consequently fine hairline cracks appeared in the rendered surface. At site level, it was decided that the uncoated, rendered walls should be painted, but first stabilised. It was believed that by sealing the surface with stabilising solution the problem of cracking would be reduced and a good surface would be provided for a water based masonry paint.
When the stabilising solution was applied to this non-porous surface it remained in a glossy condition. This can also occur when previously painted surfaces are treated in the same way.
Under these conditions, when overcoated with water-based masonry paints the adhesive properties are questionable.
The problem illustrated in this article was directly associated with this, as the adhesion of the water based masonry paint over this glassy film was poor. During periods of prolonged wetting the water based coating took up moisture and caused the paint film to swell. This moisture uptake was so much that the film sagged and when the weather changed, the film dried back exposing the stabilising solution.
Because of this, the major cost associated with the remedial works involved the removal of water based masonry paint back to stabilising solution. This was then re-coated with an oil-based masonry system which has proved to be totally successful.
Even today, examples of the same problem can be found and the illustrations shown include a situation recently found within a public building where over the years emulsion based products have been applied over an underbound coating.
Mould and Algae - Trouble Brewing
Many excellent painting projects are spoiled by the infection of mould or algae. Mould can be found on exterior
surfaces but is generally encountered inside. Different types of mould can be found but the most common can be identified by colour. The three most common types are black, green or
one with a pinkish tone.
Mould is a living fungus that thrives on substances often used in paints such as placticisers and cellulose thickeners that are incorporated in water-borne products. In addition to this, any substance that contains vegetable oils can also encourage growth. To make matters worse, the spores are airborne and can settle onto a partially formed paint film .
When work is undertaken black mould can often look like dirt and if not fully removed prior to painting the spores can be encapsulated within the wet coating. If this does occur, very soon after the work has been completed the growths can re-appear. It is because of this that when removal of the spores is eventually attempted, the paint film can be stained. This is most noticeable on whites and pastel shades.
Mould is often referred to as mildew and can survive and grow in damp rooms such as bathrooms, laundries, breweries and cellars. Factors that can also encourage mould growth include areas where the relative humidity is in the region of 75% plus.
Therefore a combination of high humidity, lack of light and lack of air flow is an ideal environment for this type of problem to be prevalent and is particularly noticeable when standard emulsion paints are used. The absorbency of the surface can also have a bearing on this matter, whether it be smooth or textured, painted or untreated. While water based coatings have fungicides incorporated within their formulations they should not be confused with specialised products designed to deal with potential mould growth.
Mould growth requires light to grow, in fact it will photosynthesise in the same way as any other plant. The main problem of paint coatings being affected by algae can be related to wall surfaces that are continually damp due to defective guttering, areas at ground level subjected to continual wetting.
In all cases where mould or algae is encountered then, it is necessary during the preparation work to ensure the spores are completely killed.
Where mould and algae are present then it is important to remove all of the spores; this may involve power washing or if the spores are incorporated within the paint film , complete stripping may be necessary.
An interesting situation occured many years ago when a Brewery decided to repaint the cold storage rooms. At that time the ceiling, walls, steelwork and woodwork were all painted pale grey with the tank ends being black. The maintenance manager decided to have all the surfaces including the tank ends repainted in white.
As there did not appear to be anything untoward the contractor carried out the usual preparation tasks and painting commenced. The actual work took approximately 2 weeks and everyone was delighted with the results. Some 4 weeks after completion urgent meetings were arranged as mould was visible on all the surfaces.
It was decided that remedial work was necessary and the entire area washed down with a proprietary fungicidal wash. A programme was introduced to monitor the situation to establish where the fungi
was originating. After several days it was established that the mould growth was stemming from the tank ends. As these were metal it baffled everyone, and the tanks were said to be dry with no condensation present prior to or during painting. At a meeting the maintenance operator was asked “How did you keep the tank ends so black" "Easy", was the reply, "l used boot polish." Vegetable oil is found not only in paint, but also in boot polish.
A lesson to be learned when dealing with problems, the cause may not be the most obvious even to the experienced tradesman.
Just how deep is the problem
Over the past years translucent wood finishes have become fashionable and because of this many joinery companies supply components which can be easily treated with these finishes or with a conventional paint system.
When these natural wood finishes are used, certain problems come to light and in many cases cause the contractors additional expense. (These additional costs have been due to lack of knowledge relating to the performance of such coatings).
In most cases the problems are generally associated with the nature and condition of the original surface. Specifiers expect them to last as long as an opaque painted system but time has revealed that the overall performance depends on the nature, texture and possible pre-treatment of the timber.
Wood finishes fall into 3 categories. Low, medium and high build. In accordance with BS EN 927-1 1997 (BS6952) the low film build types are generally recognised as stains and suitable for treating fencing, cladding etc. High build products are heavily pigmented and are opaque.
Medium build finishes are generally used for treating joinery sections.
The main requirements for these finishes are that the translucent film should be flexible enough to accommodate the overall expansion and contraction of the wood and contain pigments which act as UV filter and biocides to prevent blue staining.
When delivered to site, new windows and frames from leading joinery manufacturers are invariably coated with a preservative and an initial stain coating which is light brown in colour.
Once the windows and frames have been fixed they are often left for several months before the finishing coats are applied. This original stain/basecoat may appear to be in good condition and sound enough to apply the finish. However this may not always be the case and is where the majority of problems originate. These original stain/basecoats do not offer any lasting protection against the ultra-violet sun rays therefore the UV rays can pass through and cause the timber cells to break down. This is not always visible at first sight.
As it can be seen in the illustration although the coating appears to be all right, close inspection reveals blue staining on the glazing bar. This is the first sign that the frame has been exposed to the elements and has suffered loss of UV protection. When surfaces in this condition are overcoated, the potential problems are hidden.
It may be as little as six months later that the top coat starts to show signs of deterioration. The first indication is checking of the finished film which can be either as a result of poor flexibility or due to the hidden degradation of the wood cells resulting in poor cohesion. This hidden degradation is the cause of the majority of problems.
While these coatings are designed to erode it is important that re-coating takes place before breakdown occurs. If left total erosion of the coating takes place with the timber surface becoming infected and very fibrous. When this occurs then remedial work is extensive.
It is the view of many that when translucent finishes are used then planned maintenance should be considered.
Experience has shown that elevations exposed to the maximum UV rays require much earlier attention than sheltered areas. Depending on the prevailing conditions this maintenance may be required after 18 months.
Whenever asked to comment on the performance of these translucent wood finishes and in the event of a breakdown after carefully removing the defective coating always examine the reverse side of the dry film. If on examination timber fibres are attached then it is most likely that the ultra violet rays have passed through the film , causing degradation of the timber which is the root of the problem.
Note: Although manufacturers have different products the systems normally consist of one coat of preservative/basecoat followed by 2 coats of the finishing product. When reading the manufacturers' data, in the majority of cases their literature refers to these products being applied onto new planed timber and do not always make reference to overcoating stained joinery as supplied to sites. As always it is advisable to consult with the manufacturer beforehand.
Blistering Headache
The early to mid-1970s was a boom time for our industry with the design and build concept being accepted by many local authorities. This surge in building has now brought many problems, largely associated with the type and nature of the building materials used along with the basic design of the various components, such as windows. The component parts of these modular type buildings - mainly schools and housing - were in many cases part assembled in the factory and transported to site. This procedure resulted in the cavity membrane and insulation being disturbed. This also applied to the earlier timber framed dwellings that are now quite commonplace.
Although many of these buildings were subsequently cladded with traditional materials such as brick, sand/cement render or wood, the moisture created internally can still be absorbed into the interior surface and transferred through to the exterior surface.
If we look at the joinery and in particular the window design, we can see that the detail of the various components have gone from having a good rebate with arises rounded off to sections that are almost level. This is particularly noticeable with the window cills having gone away from a good rounded nose to almost square angles.
we encounter are of poor design with no proper sealant being used before fixing the glazing beads and wire nails which are inclined to corrode have been used in place of brass screws. Consequently water ingress readily occurs.
General poor maintenance and the failure to replace old putties is also a major problem.
It could also be argued that a double glazed sealed units contribute towards a high moisture content of the building fabric.
Because of the high moisture content in many buildings, and ingress of water due to the poor design details, a breakdown of exterior coatings is not unusual. This occurs not only on the timber windows but also on masonry.
Blistering of the paint coatings is one of the first signs with the illustration being an example of the extent to which this problem can develop.
In this case the cladding has not been back primed and coated prior to fixing g. Due to normal expansion water ingress has occurred between the joints and has been absorbed into the unprimed wood. Because of the high moisture content and lack of moisture transfer through the conventional paint coating the water pressure behind the film has caused the blister.
As this problem has been recognised by numerous manufacturers they have incorporated microporous coatings within their product portfolios. This terminology is also referred to as 'moisture permeable coatings' or 'breathable paints'. These products can be of various formulations ranging from water-based acrylics, alkyd resins or a combination of alkyd and acrylic. All of these paints will allow a much higher percentage of moisture vapour to pass through the dry paint film, and so reduce the likelihood of the type of problem illustrated. For these products to be totally effective it is essential that on refurbishment work all of the existing coatings are removed back to the natural substrate.
Tests carried out have shown that on average 0.26 gms of water vapour is transmitted per hour,per sq.m where conventional alkyd paint has been used. However up to 1.45 gms is transferred at the same rate where microporous coatings have been used.
Water vapour transmission is not only criterion to be considered as the paints to be used must be suitable for the type of surfacing to be coated. For example acrylic finishes allow a maximum vapour transmission but alkyd finishes may give better adhesion.
Generally the sheen level of microporous coatings used on woodwork is not as high as the traditional gloss finishes therefore it is important for those considering using this type of product to highlight this to their clients.
As always prudent to consult the manufacturer's representative when faced with problems such as this to ensure the correct system is used.
Don't let flooring problems trip you up
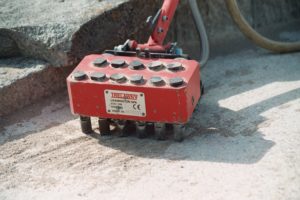
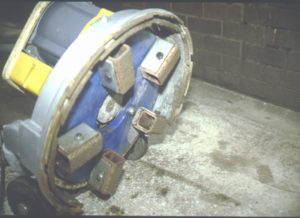
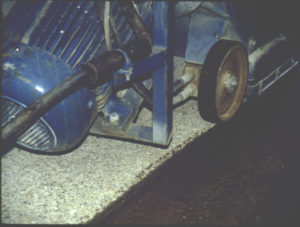
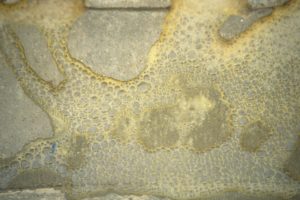
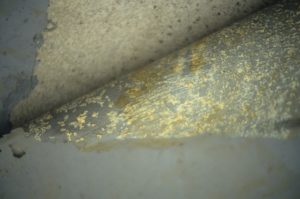
Don't let flooring problems trip up up
Due to health and safety, or for decorative reasons, more and more maintenance managers are requesting painting contractors to carry out floor treatments.
Before considering the type of floor coating to be applied (single or two) the condition of the existing substrate should be foremost in the minds of the customer/specifier and contractor.
In the first place, the moisture content of the substrate should be checked. This should be no higher than 5%. The best way of checking this is by using a moisture meter specifically designed for this purpose.
Companies who regularly carry out work of this nature have these moisture meters available. However, those who only occasionally carry out this type of work and do not have a suitable meter can still check if there is high moisture content within the substrate. To do this, pieces of clean polythene should be placed in various locations over the existing surface and the edges sealed with tape. After 24 hours if the clean film is only misted over then it should be okay to proceed. If however, there are actual water droplets present then the moisture content is likely to be higher than 5%.
If this is the case then a suitable membrane is going to be required. This could be a special bitumen based coating which must be compatible with the finishing material. More drastic measures may be necessary such as covering the surface with asphalt or even applying a polythene membrane followed by re-screeding with sand and cement.
Once the matter relating to the moisture content has been resolved then the preparation needed is equally important. There are three common methods of preparing floors prior to applying a paint system. Acid washing is using a solution of hydrochloric acid which effervesces (bubbles) and burns off the top layer of the cementitious surface.
This method, although extremely economical, can present certain problems when working in a close environment because of the dangerous fumes. Working above ground level where no drainage system is available also presents problems because the acid needs to be neutralised with clean water once the effervescence has subsided. Where this wet system cannot be used then dry methods are recommended .
Grit blasting or scabbling/planing.
These two systems are looked upon with some degree of apprehension however, the specialised machines are dust free, easy to manoeuvre, safe and highly accurate. Therefore they can prove to be the most cost effective and trouble free. These machines have built in extractor units which separate the debris from the grit which is then recirculated. The size and type of machine to be used is relative to the area to be treated. These grit blasting machines can prepare areas of up to 180m2 per hour which can prove to be more economical than using a wet system.
The major advantage of this type of preparation is that painting can commence instantly whereas, with hydrochloric acid, the surface must be allowed to dry.
For small areas including stair treads, hand tools with extractor units are also available.
Don't be mis-led when presented with new floors, particularly power floated surfaces as, irrespective of the perceived condition, they all need to be prepared. Another danger is that some concrete floors when laid are treated with a clear sealer, many of which reject paint coatings. Therefore this sealer if present should be removed by one of the dry systems. Any surface that has been previously painted or sealed is unaffected by the hydrochloric acid. The treatment of floors heavily contaminated with oil should be avoided and specialists brought in to deal with such circumstances. Any making good to be carried out should always be with a suitable product which is compatible with the main substrate such as epoxy mortars or cement mixed with latex polymer.
It should be acknowledged that where slip-resistant surfaces are required then the cleaning will be more difficult than a smooth surface.
Time spent in discussion with your clients to establish their needs and expectations will always ensure the correct product is used. Once this has been firmly established then it is wise to consult with the manufacturer of the products to be used. An extra hour of your time dealing with this will pay dividends.