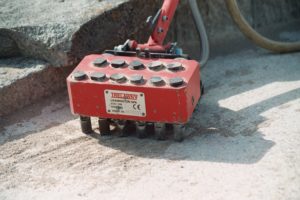
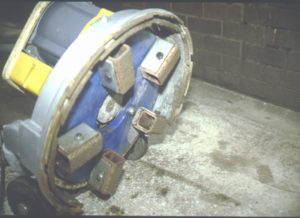
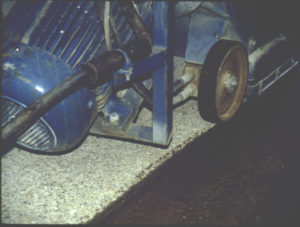
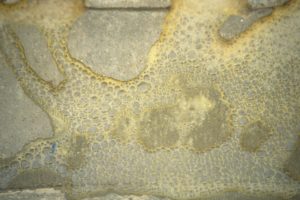
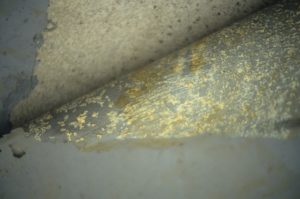
Don’t let flooring problems trip up up
Due to health and safety, or for decorative reasons, more and more maintenance managers are requesting painting contractors to carry out floor treatments.
Before considering the type of floor coating to be applied (single or two) the condition of the existing substrate should be foremost in the minds of the customer/specifier and contractor.
In the first place, the moisture content of the substrate should be checked. This should be no higher than 5%. The best way of checking this is by using a moisture meter specifically designed for this purpose.
Companies who regularly carry out work of this nature have these moisture meters available. However, those who only occasionally carry out this type of work and do not have a suitable meter can still check if there is high moisture content within the substrate. To do this, pieces of clean polythene should be placed in various locations over the existing surface and the edges sealed with tape. After 24 hours if the clean film is only misted over then it should be okay to proceed. If however, there are actual water droplets present then the moisture content is likely to be higher than 5%.
If this is the case then a suitable membrane is going to be required. This could be a special bitumen based coating which must be compatible with the finishing material. More drastic measures may be necessary such as covering the surface with asphalt or even applying a polythene membrane followed by re-screeding with sand and cement.
Once the matter relating to the moisture content has been resolved then the preparation needed is equally important. There are three common methods of preparing floors prior to applying a paint system. Acid washing is using a solution of hydrochloric acid which effervesces (bubbles) and burns off the top layer of the cementitious surface.
This method, although extremely economical, can present certain problems when working in a close environment because of the dangerous fumes. Working above ground level where no drainage system is available also presents problems because the acid needs to be neutralised with clean water once the effervescence has subsided. Where this wet system cannot be used then dry methods are recommended .
Grit blasting or scabbling/planing.
These two systems are looked upon with some degree of apprehension however, the specialised machines are dust free, easy to manoeuvre, safe and highly accurate. Therefore they can prove to be the most cost effective and trouble free. These machines have built in extractor units which separate the debris from the grit which is then recirculated. The size and type of machine to be used is relative to the area to be treated. These grit blasting machines can prepare areas of up to 180m2 per hour which can prove to be more economical than using a wet system.
The major advantage of this type of preparation is that painting can commence instantly whereas, with hydrochloric acid, the surface must be allowed to dry.
For small areas including stair treads, hand tools with extractor units are also available.
Don’t be mis-led when presented with new floors, particularly power floated surfaces as, irrespective of the perceived condition, they all need to be prepared. Another danger is that some concrete floors when laid are treated with a clear sealer, many of which reject paint coatings. Therefore this sealer if present should be removed by one of the dry systems. Any surface that has been previously painted or sealed is unaffected by the hydrochloric acid. The treatment of floors heavily contaminated with oil should be avoided and specialists brought in to deal with such circumstances. Any making good to be carried out should always be with a suitable product which is compatible with the main substrate such as epoxy mortars or cement mixed with latex polymer.
It should be acknowledged that where slip-resistant surfaces are required then the cleaning will be more difficult than a smooth surface.
Time spent in discussion with your clients to establish their needs and expectations will always ensure the correct product is used. Once this has been firmly established then it is wise to consult with the manufacturer of the products to be used. An extra hour of your time dealing with this will pay dividends.